总体参数
—规格 GBZ1600×10000mm
—输送物料 金矿
—-大物料粒度 mm 80
—设备重量 t ~45
—喂料宽度 mm 1600
—头尾轴中心距 mm 10000
—输送速度 m/s ~0.09
—功率 kW 45
GBZ1600×10000重型板式给料机托轮及槽板的技术改进
改造原因:上、下托轮组的使用寿命-长不到3个月,-短只有半个月,且更换困难,每次更换一套托轮组需40多h。
一:存在的问题及原因分析
(1)由于托轮组的支撑梁在槽板下纵横交错,极易积矿,导致托轮无法转动而摩擦损坏。
(2)托轮数量多(共 162 组)且无法加油润滑。托轮布置在槽板下部,无法进行点检。
(3)因托轮轴承承载能力不足,当槽板与给料机侧板之间夹矿时,托轮承载力瞬间增加,极易造成托轮损坏。
(4)槽板上的加强肋板极易挂矿,当槽板行至下部回程时,矿石脱落堆积到下托轮支撑梁上。运行过程中,肋板还会推压夹在侧板与槽板之间的矿石,对大罩侧板的下沿起切削作用,从而加速了侧板的磨损。该矿对槽板结构进行了改进,将两侧10mm长的肋板割除,向下加长衬板,并减小衬板与槽板之间的间隙,但槽板和侧板之间形成 90°夹角,仍存在夹矿现象。
二:改进后的槽板结构
(1)托轮轴承座外移至给料机大梁处,并加装润滑油杯,便于润滑与点检。
(2)上托轮结构改进:
①板式给料机尾部位于粗碎料仓下方的8组托轮组,由于下料时承受较大的冲击力,托链轮采用整体结构,与轴采用φ122H7/m6过渡配合,轴向采用轴肩+轴用钢丝弹性挡圈定位。支重轮与轴采用φ128H7/m6过渡配合,轴向采用轴肩+顶丝定位。由于托轮组轴向跨距较大(2170mm),托轮组在大弯矩、小扭矩的工况条件下工作,因此采用GB/T1566—1979薄型平键传递扭矩,并选用22218C圆柱滚子轴承。
②前、中部10组上托轮组、托链轮采用对开结构,上、下部用4条M12×45内六角螺栓联接,与轴采用φ128 H7/h7间隙配合,轴向采用轴肩+轴肩定位。托轮采用对开结构,在不拆卸轴及轴承的情况下即可更换托链轮,支重轮与轴的装配及轴承、平键的选用同尾部上托轮组。
(3)下部托轮组托轮采用对开结构,上、下部用4条M22×85双头螺栓联接。螺母选用GB6184-2000Ⅰ型全金属锁紧螺母,确保联接的可靠性。托轮与轴采用φ128H7/h7间隙配合,轴向采用轴肩+轴肩定位。支重轮与轴的装配及轴承、平键的选用同上。
(4)下托轮的支撑位置由原槽板侧板下沿位置改为槽板平面与链节的固定部位,以避免托轮对槽板侧板下沿的磨损,提高槽板的使用寿命,减少漏矿。
(5)大罩衬板的材质由原Q235-A改为ZG45,并对下部35mm范围(易磨损部位)进行局部淬火,硬度为 HRC48~52,以延长衬板的使用寿命。
(6)去除槽板上的加强肋板,将槽板底板的厚度由20mm改为25mm,并加宽凸台,使槽板与大罩衬板下沿相对运动部位的缝隙上移。槽板凸台与大罩衬板下沿的设计间隙为8~10mm,当衬板磨损后,可以在轴承座下加装调整垫片来调整间隙,-大调整高度为30 mm。控制好该间隙也可减少夹矿或减小夹矿的粒度,以减轻夹矿带来的危害。
三:板式给料机改进效果
改进前,托轮的使用寿命为3个月,单台套托轮备件10.40 万元;衬板的使用寿命为1.5个月,单台套备件2.187万元,全年维修费用共计59.1 万元。改进后,托轮的使用寿命为6~8个月,单台套托轮备件6.03 万元;衬板使用寿命为6个月,单台套备件4.53万元,全年维修费用共计10.56 万元。
改进后有效减少了给料机的故障率,提高了系统运行的可靠性,减少了维修成本与维修时间.
电话:13606279786
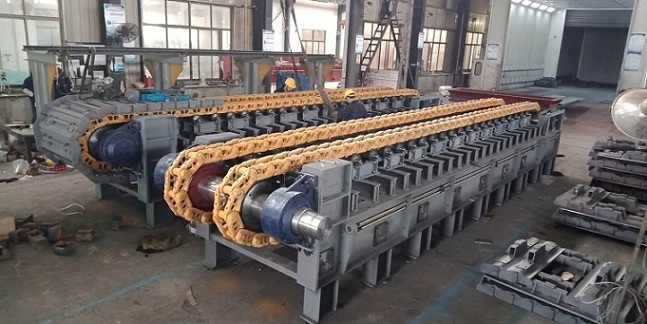


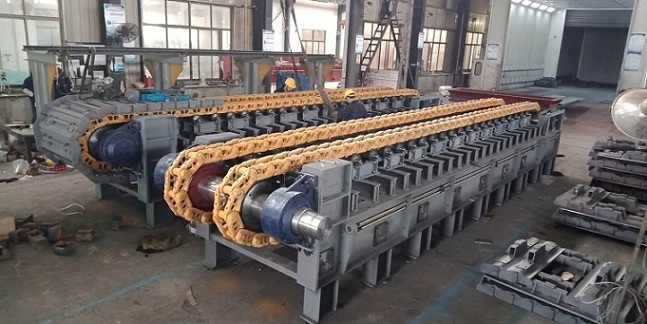

